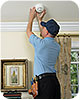
Carbon monoxide detectors are becoming an increasingly common element in fire and intrusion protection alarms for both residential and business customers. This rise has been driven, in part, by regulatory requirements and in part by dealers who just think it’s a good idea to propose CO detection for every installation.
In this article, we look at the changing regulatory environment for CO detection and how security dealers can best position themselves for success in selling and installing CO detection.
CO DANGERS
Carbon monoxide is an odorless, colorless and highly toxic gas that results from the incomplete burning of fossil fuels. Common sources of CO are improperly vented furnaces and car exhausts. People exposed to small amounts of carbon monoxide may experience headaches and, as CO levels rise, may become drowsy and even unconscious. Ultimately, if CO levels continue to rise, the substance can be lethal.
CO detectors are designed to provide early warning of unhealthy CO levels. Twenty-nine states now have some type of regulatory requirement for CO detection for new installations, according to alarm equipment manufacturer System Sensor of St. Charles, Ill. “In the next three to five years, you’re going to see the number of states having a mandate go up,” predicts Richard Roberts, industry affairs manager for System Sensor.
Local authorities having jurisdiction (AHJs) are responsible for enforicng statewide requirements and also may add their own CO detection requirements. State and local requirements often are driven by NFPA 720, a code developed the National Fire Protection Agency that focuses specifically on CO detection, and by the International Fire Code, International Building Code and International Residential Code developed by the International Code Council (ICC).
As Roberts explains, the International Residential Code applies to single- and two-family dwellings and townhomes with no more than three stories and has required CO detection beginning with the 2009 version. The 2012 version of the International Building Code, which Roberts says is close to being finalized but will not be published until next year, requires CO detection for hotels, motels, apartments, dormitories, convalescent centers and the like.
There is some overlap between NFPA and ICC requirements, Roberts notes, but in general, he says, the ICC codes specify when CO detection is required whereas NFPA 720 is an installation standard that describes how CO detection equipment is to be installed, tested, inspected, maintained and monitored.
Both the NFPA and the ICC update their requirements every so many years. But typically not all AHJs adopt the latest versions of the NFPA 720 or the ICC codes right away, sometimes lagging by several years.
The scope of NFPA 720 has covered CO detection in dwelling units for some time. But as Tom Mechler, product marketing manager for Fairport, N.Y.-based manufacturer Bosch Security Systems, explains, the scope of the 2009 version of the standard expands beyond dwelling units to apply to other buildings and structures. These include hotels, rooming houses, dormitories, day care facilities, schools, hospitals, assisted living facilities and nursing homes. The upshot, as Mechler explains, is that those dealers that “have primarily done business commercially and haven’t thought a lot about CO detection will have to start thinking about it.”
SELLING MONITORED CO DETECTION
Often AHJs do not require CO detectors to be monitored. But when bidding on a business or residential job, dealers should be able to make a strong case for including CO detection as part of a monitored fire and intrusion alarm system.
When a stand-alone CO detector goes into alarm, some people, particularly children or elderly people, may not know what the next step is, notes Mike Garavuso, product manager for Melville, N.Y.-based manufacturer Honeywell Security. “If the system includes CO detectors and is monitored, central station operators will take the necessary steps and dispatch fire or police to come and make the necessary actions,” Garavuso describes.
EQUIPMENT REQUIREMENTS
Some AHJs may have requirements that impact the type of CO detector that can be installed in a home or business. For example, the AHJ may require the detectors provide an alert as they approach the end of their life.
Unlike a smoke detector that may function fine for 10 years or more, CO detectors have sensors, notes Tim Frankenberg, fire product manager for St. Louis-based equipment manufacturer Potter Electric Signal Company. “Any time you have a sensor, you have a finite life,” explains Frankenberg. To help ensure that sensors are working properly, some manufacturers, including Potter, have a self-monitoring capability, automatically generating an alert if a problem with the sensor is detected.
Moving forward, dealers are increasingly likely to encounter that requirement along with some additional requirements for CO detector installations.
Mechler notes, for example, that the 2009 version of NFPA 720 requires a CO alarm to be annunciated in a different way than a fire alarm. “Audibly and visually it must be different,” he says, adding that Bosch offers a control panel that uses a blue LED and unique audio tone to indicate a CO event.
Another new requirement goes into effect the first of the year in 2012. The 2009 version of NFPA 720 requires technicians beginning as of that date to conduct a functionality test when they complete a CO detector installation, Roberts notes. “You must functionally test the detector to ensure proper operation through the introduction of CO gas into the sensing chamber,” he explains. “No longer will pushing a button on the detector suffice. You must spray gas into the chamber.”
CO detectors are undergoing a redesign to support this type of test capability, notes Roberts, who adds that System Sensor already offers a CO detector that can support the new requirement. Although some AHJs may not require the test at the January 1, 2012 start date, manufacturers will likely want to make sure that all CO detectors sold by late 2011 are able to support the testing capability.
A CO Detector Installation Myth
When dealers first began installing CO detectors, it was commonly believed that the detectors should be installed near the floor. But today many people in the industry question that belief.
“There’s a lot of misunderstanding about where detectors should be placed,” comments Justin Mayer, product manger for System Sensor. “People thought carbon monoxide came in low and stayed there. There was a misunderstanding about how it fills up a room. It doesn’t rise or fall.”
It’s now common practice to install CO detectors higher up on a wall or even on a ceiling, Mayer notes.
Tim Frankenberg, fire product manager for Potter Electric Signal Company, agrees. “Mounting them on the ceiling is good, or at about the five- or six-foot mark.”
Because people are most vulnerable to the effects of carbon monoxide poisoning when they are asleep, it’s also recommended that CO detectors be installed in or just outside of bedrooms, note Mayer and Frankenberg. If a home has an attached garage, it’s is a good idea to install CO detection in the home in the immediate vicinity of the garage, thinks Richard Roberts, industry affairs manager for System Sensor.