If there is one good thing that has come out of this forced “down time” due to the coronavirus, it has been the opportunity to spend some time learning new skills. While personal growth has been a popular go-to, security dealers and integrators also looked to the internet for more job-specific enhancement. When it comes to security locks and door hardware, there is no shortage of training videos, both on YouTube and through individual manufacturer’s and distributor’s sites.
While such training is not new, what has changed is the numbers and types of people seeking it, says Glen Davies, learning leader, dormakaba USA Inc., Indianapolis. “We have seen a change in demographics. Since it is all done online now and we can track through the platform, we are seeing a lot more sales reps from companies, including a lot of installers we don’t typically have attend classes.” These include commercial installers, institutional locksmiths and even some integrators, he says. “We have seen that ever since the mandatory lockdowns, a lot of folks were not able to go out to customer sites, so without that travel time there was more time to spend learning. We have absolutely seen a huge increase in that.”
Top Tips
SDM asked the experts for their No. 1 top tech tip for a smooth security lock installation. Here are a few of their responses:
1. Plan ahead. “This is the same thing I tell my sales teams. They don’t plan to fail, but fail to plan. Review the product and bench test it if at all possible. Have a complete understanding of what the customer is trying to accomplish with your solution. This allows for a seamless installation on the site. — Bill Smoyer, Access Hardware Supply
2. Get familiar. “I think the top tech tip I would give would be that if they are not familiar with the type of lock and how it is installed, take the time to get familiar with the installation procedures. Installation jigs are a time saver and make for a smooth installation.” — William Sporre, senior vice president of sales, Alarm Lock – Marks USA, divisions of NAPCO Technologies, Amityville, N.Y.
3. Be a specialist. “Stick with a standard set of tools and become a specialist in a specific set of hardware instead of trying to be a jack of all trades. Your knowledge for a specific toolbox will result in better quality work that can be done faster, which will benefit you and the customer.” — Will Rehlich, head of hardware, Nexkey Inc., San Mateo, Calif.
4. Bring painter’s tape. “Painter’s tape can be used as a medium for making measurements on doors and frames for security locks and hardware, and of course a sharp pencil. The tape aids in seeing the template marks, while protecting the door and frame from scratches that can be caused during installation.” — Chad Tibbets, training specialist, ASSA ABLOY Academy, ASSA ABLOY, New Haven, Conn.
5. Use a screwdriver. “A common mistake is using a drill. They think it will speed up the installation, but it actually ends up over-tightening the lock and binds it down, making it so it doesn’t perform optimally if it doesn’t actually break it. A simple screwdriver is all that is needed to correctly install it.” — Nick English, Kwikset
6. Read the instructions. “It’s pretty low-tech, but they should take it on themselves to understand procedures before they go to install it. Read instructions all the way through; highlight the areas that stand out and go through it again. A lot of folks don’t want to be seen on the job site reading instructions, so take the time to do it in advance.” — Glen Davies, dormakaba
7. There might be an app for that. “Paper templates and instructions tend to get lost on job sites. Smartphones have made finding information much easier for the installer. [Our customer support app] turns the installer’s smartphone into a library for all installation templates, instructions, wiring diagrams and catalogs, and provides a portal for face-to-face technical support from our factories. Having these assets at your fingertips takes the guesswork out of installations.” — Chad Tibbets, ASSA ABLOY
Nick English, national sales manager, Kwikset, Lake Forest, Calif., has seen similar trends, and also notes an increase in salespeople taking online training about products and installations. “We have definitely seen an uptick in companies getting ready to have their installers and salespeople hit the road running full steam when they are able to get back out,” he says.
“The economy was so strong before COVID-19 that training was considered a luxury, even at our company,” adds Bill Smoyer, national sales manager for Access Hardware Supply, San Leandro, Calif. “Now companies must invest in training to reduce installation and service time.”
Though things are starting to “normalize” and business will hopefully pick back up, the need for training is more important than ever, says Tom Welham, director, integrator channel strategy, Allegion, Carmel, Ind. “While these courses have been offered on an ongoing basis, even prior to COVID-19, amidst the current situations, these training opportunities are an increasingly important way for users to stay informed of the latest industry trends and continue improving their own skills. As we look toward changes that may arise as a result of the pandemic, training courses will play an even larger role in ensuring that integrators, operators and other professionals are prepared and knowledgeable about the latest standards required and solutions available, with access to insight at the tip of their fingers.”
The good news is that the vast majority of training offered by manufacturers or distributors is free and easy to find. Many can even be found on YouTube at your leisure. Here are a few of the key tips from trainers, along with some links to get you started.
Training Videos
SDM also asked for some short videos that exemplify the information and training that is available online. There are many more where these came from, and most can be found on YouTube, or on the manufacturer’s website.
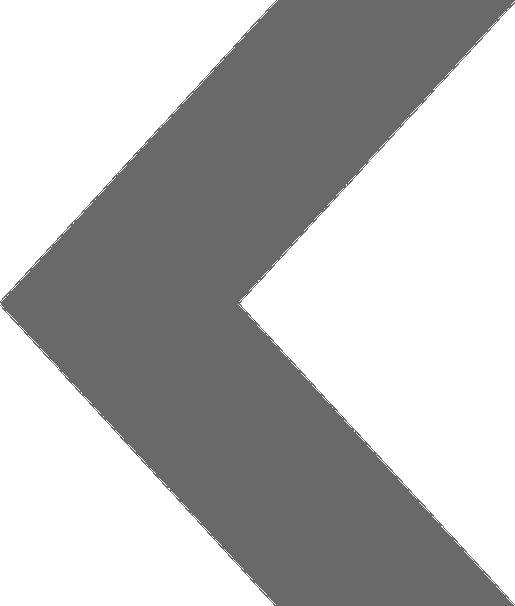
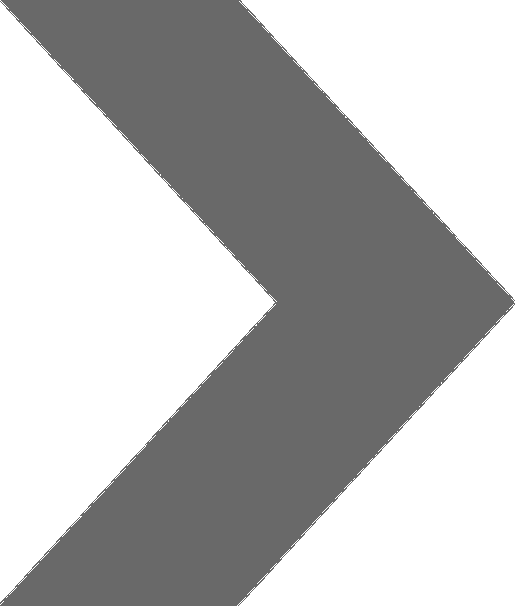
Kwikset's YouTube Page
www.SDMmag.com/videos-Kwikset-smartcode
ASSA ABLOY's Video Page
www.SDMmag.com/videos-assaabloy-door-closer
Allegion's YouTube Page
www.SDMmag.com/videos-allegion-door-hardware
Camden's YouTube Page
www.SDMmag.com/videos-camden-kinetic
Napco's YouTube Page
www.SDMmag.com/videos-alarm-lock-trilogy
Access Hardware Supply's YouTube Page
www.SDMmag.com/videos-access-hardware-von-duprin